Efficient Rotary Cap Compression Moulding Machine
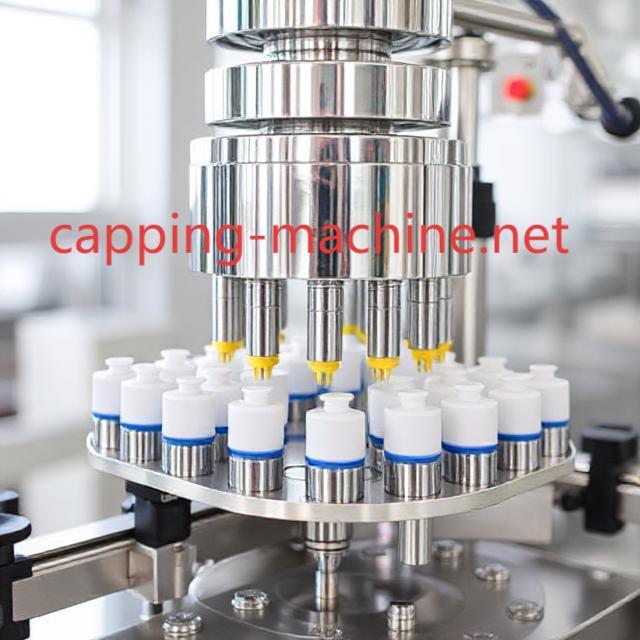
As demand for high-speed, precision-based cap production continues to grow, the Rotary Cap Compression Moulding Machine has become a go-to solution for manufacturers seeking scalable and efficient solutions. Designed for continuous and consistent output, the Rotary Cap Compression Moulding Machine offers a range of benefits, including low energy usage, reduced material waste, and greater cap quality uniformity. Taizhou Chuangzhen Machinery Manufacturing is one of the few specialized producers delivering these high-performance machines tailored to modern industrial needs.
Unlike injection molding, rotary compression molding uses a unique principle. Thermoplastic resin is heated and directly compressed into individual mold cavities that rotate around a central axis. Each station works independently, which helps maintain uniform heat distribution and molding pressure. This results in caps with excellent sealing ability, strong structural integrity, and consistent dimensions. The rotary system enhances production efficiency by enabling simultaneous heating, molding, and cooling in different stations across the carousel-like setup.
The machine’s versatility makes it ideal for producing caps for bottled water, carbonated beverages, edible oil, and pharmaceutical containers. It supports various cap designs, including flat caps, flip-tops, and tamper-evident types. Taizhou Chuangzhen offers machines with multiple cavity options, allowing manufacturers to choose the right configuration based on production volume and product specifications. Quick mold change features and modular component design help reduce downtime during changeovers, improving operational continuity.
One of the key technical advantages is its lower molding temperature and shorter cycle time compared to injection systems. This contributes to significant energy savings and minimizes thermal stress on the material, which in turn leads to improved cap clarity and durability. Chuangzhen’s machines also incorporate servo-driven systems that ensure precise synchronization between molding actions and the rotating platform. These features allow operators to achieve higher output with better control over product quality.
Modern rotary cap compression machines also embrace smart automation. Chuangzhen integrates PLC controls, touchscreen HMIs, and automatic feeding systems to simplify operation and monitoring. Parameters such as mold temperature, compression pressure, and cycle duration can be precisely adjusted and monitored in real-time. Sensors detect any deviation from set parameters, alerting the operator and reducing defective output. This level of automation reduces labor dependency and enhances consistency across large production batches.
In addition to performance, durability plays a crucial role in manufacturing decisions. Chuangzhen uses high-grade stainless steel frames and international-standard components to ensure long-term operational stability. Maintenance access points are strategically placed to support quick inspection, cleaning, or part replacement. Combined with comprehensive after-sales technical support, these machines offer long service life and minimal disruption to operations.
For manufacturers aiming to upgrade their cap production lines with reliable, energy-efficient equipment, Taizhou Chuangzhen Machinery Manufacturing provides a robust range of rotary compression molding machines. For detailed specifications and customization inquiries, visit: https://www.capping-machine.net/ .
- Art
- Causes
- Crafts
- Dance
- Drinks
- Film
- Fitness
- Food
- Spellen
- Gardening
- Health
- Home
- Literature
- Music
- Networking
- Other
- Party
- Religion
- Shopping
- Sports
- Theater
- Wellness